An Introduction to Carbon Fiber
Carbon fiber—"the world's structural wonder material"—is also known as graphite fiber. It is a very lightweight and very strong material. In comparison with steel, it is five times stronger and two times stiffer and lighter, which makes it an excellent manufacturing material for several parts. Engineers and designers prefer carbon fiber for manufacturing.
Properties of carbon fiber:
- High strength-to-weight ratio
- Good rigidity
- Corrosion-resistant
- Electrically conductive
- Fatigue resistant
- Good tensile strength but brittle
- Fire resistance/not flammable
- High thermal conductivity
- Low coefficient of thermal expansion and low abrasion
- Nonpoisonous
- Biologically inertness and X-ray permeability
- Self-lubricating
- Excellent electromagnetic interference shielding property
- Relatively expensive
- Requires specialized experience and equipment to use
- High dimensional stability, low coefficient of thermal expansion, and low abrasion
- High damping
- Electromagnetic properties
These fibers are not used as such. They are used to reinforce materials such as epoxy resins and other thermosetting materials. These materials are termed composites as they possess more than one component and are quite strong for their weight. They are very strong in comparison with steel but very much lighter. Due to this property, they may be used to replace metals in several applications, from parts for airplanes and the space shuttle to tennis rackets and golf clubs.
Advantages of carbon-fiber-reinforced carbon composites:
Resistance to high temperatures and weathering, low flammability, low smoke density, and low toxicity of decomposition products. Temperature resistance of course depends on the choice of resin
High chemical stability
A large variety of possible component shapes and sizes
High durability due to long prepreg storage life
Prepregs comprise the range of reinforcements and resin matrix combinations. They are manufactured on a state-of-the-art fusible resin plant. Fusible resins have fewer volatile constituents and increase the composite materials’ mechanical strength. The prepreg manufacturing plant is accredited to DIN ANDISO 9001 quality assurance standards
History:
Carbon fibers date back to 1879. Thomas Edison baked cotton threads or bamboo silvers at elevated temperatures, which carbonized them into an all-carbon-fiber filament. In 1958 Roger Bacon of Ohio in Cleveland, Ohio, United States, produced high-performance carbon fibers. Leslie Philips, a British engineer, 1964, realized the high strength of carbon fiber. Later on, carbon fibers produced from rayon strands processed by carbonation were developed. Akio Shindo in the early 1960s produced carbon fibers from PAN. For manufacturing PAN-based carbon fibers, PAN is processed to a fibrous shape by spinning and then subjected to oxidation, carbonization, and surface treatment. Leonard Singer produced carbon fibers from the pitch in 1970. The manufacturing process involves making petroleum or coal pitch into a fibrous shape; then oxidation, carbonization, and surface treatment are performed (Saito et al., 2011). These fibers were not efficient and contained about 20% carbon. The strength and stiffness properties were inferior. The US Air Force and NASA started using carbon fiber in aircraft and spacecraft applications.
Applications Overview:
Nowadays, carbon fibers have become an important part of several products, and new applications are being developed. The leading producers of carbon fibers are the United States, Japan, China, and Western Europe. Worldwide carbon fiber is in rapidly growing demand as a lightweight and strong alternative to metal for various industries such as aeronautics, automotive, marine, transportation, construction, electronics, and wind energy. Carbon nanofibers have been explored for use in regenerative medicine and also for the treatment of cancer. Applications in aerospace and defense, the sport/leisure sector, and wind turbines have grown substantially. The automotive segment is also becoming very important. This could be because of the ramp-up phase for the production of the i-models from BMW. Other applications are the construction of molding and compounding plants, pressure vessels, civil engineering, and marine.
Global carbon fiber demand by application in 1000 tons (2013) (total 46,500 t).
Aerospace and defense Molding and compound Sports and leisure Wind turbines Automotive Pressure vessels Civil engineering Marine Others |
13.9, 30% 5.5, 12% 6.4, 14% 6.7, 14% 5.0, 11.0% 2.4, 5% 2.3, 5% 0.8, 2% 0.5, 7% |
Based on Holmes M. Global carbon fiber market remains on an upward trend.
Reinf Plast 2014;58:38–45
Trends of Carbon Fiber Consumption:
The diameter of carbon fiber is about 0.0002–0.0004in. and contains at least 90% carbon by weight. It is a long, thin strand of material. The carbon atoms are bonded together in microscopic crystals. These are more or less aligned parallel to the long axis of the fiber. The crystal alignment makes the fiber very strong for its size. Thousands of carbon fibers are twisted together to form a yarn. This can be used by itself or woven into a fabric. The yarn or fabric is blended with epoxy and wound or molded into shape for producing different types of composite materials. Carbon fiber-reinforced composites are being used for making aircraft and spacecraft parts, racing car bodies, golf club shafts, bicycle frames, fishing rods, automobile springs, sailboat masts, and several other components where lightweight along with high strength is required.
Several types of carbon are available. They can be sort or continuous. These are crystalline, amorphous, or partly crystalline. The below chart shows the estimated global carbon fiber consumption
Carbon fibers were used successfully on a commercial scale in the early 1960s, as the need of the aerospace industry—especially for military aircraft—for better and lightweight materials became very important. In this process, polyacrylonitrile was used as a starting material. This process produced a carbon fiber that had very good strength properties. Therefore the polyacrylonitrile process rapidly became the main method for manufacturing carbon fibers.
“Carbon fibers are being used widely in commercial and civilian aircraft, recreational, industrial, and transportation markets. Carbon fibers are used in composites with a lightweight matrix. Carbon fiber composites are particularly suited for applications where strength, stiffness, lower weight, and outstanding fatigue characteristics are the main requirements. They can be also used where high temperature, chemical inertness, and high damping are important, Carbon fibers offer 10 times the strength of steel at a quarter of the weight” Said CFG
Carbon Fiber Types:
Carbon fibers manufactured from polyacrylonitrile have better mechanical and physical properties in comparison with rayon-based ones. Today, they are the most promising raw materials for the production of high-strength carbon fibers. Carbon fibers based on mesophase pitch turned out as more expansive following a complicated and complex process of conversion of cheap pitches into mesophase-forming modification.
The below data shows the market share of carbon fibers depending on the precursor type:
PAN—carbon yield 50%; middle/high modulus; high/very high strength Market share, 95%
Mesophase pitch—carbon yield 80%; very high modulus; low/middle strength Market share <5%
Cellulose—carbon yield 25%; poor because internal defect structure Market share, minimal
Lignin—carbon yield 20%; poor because internal defect structure Market share, minimal
Based on Fitzer E, Heine M. Carbon fibers in a book: Industrial carbon and graphite
materials—Raw materials, production, and applications. [in print] Wiley-VCH; 2019.
Carbon fiber-reinforced polymer or carbon-fiber-reinforced plastic(CFRP) is a highly desired, high-value material showing superior strength-to-weight properties. Polyepoxide (epoxy) is the polymer mostly used, but other polymers such as vinyl, nylon, ester, or even polyester can be used in a few cases. Other fibers such as glass fibers, Kevlar, and aluminum can also be used along with carbon fibers. Carbon fiber can be classified in different ways, such as by raw materials and mechanical properties. Raw materials can be divided into polyacrylonitrile carbon fiber, pitch carbon fiber, and rayon carbon fiber. Currently, the majority of structural materials are using polyacrylonitrile carbon fiber. Mechanical properties are divided as follows :
(1) ultra-high modulus (UHM) carbon fiber
(2) high modulus (HM) carbon fiber
(3) ultrahigh strength (UHS) carbon fiber
(4) high strength (HS) carbon fibers
Carbon fiber composites have remained an elusive material in the automotive industry. These have been used in jet fighters and high-end race cars for more than 20 years, so there is very little doubt about their ability to build lighter and more durable vehicles. Carbon fiber offers a weight savings of 75% over steel. These fibers give sports cars a real benefit in acceleration and top speed and enable all automobiles for obtaining improved fuel economy. “Since 1960, the carbon fiber business has grown in volume. The main markets that have driven this growth are the following industry:
• Aerospace wind energy
• Compressed natural gas storage
• Civil engineering”
During the last decade, several important changes have taken place in the carbon fiber industry. During 2005–06, there was a shortage of carbon fiber. But the market situation rapidly changed because of the economic downturn worldwide. The demand dropped in the first three quarters of 2009 as the economy worsened worldwide. At the same time, supply increased and some producers had a sufficient supply of carbon fibers with lower lead times to consumers. “The global carbon fiber market has grown at double digits during the last five years and would grow at a slower speed, increasing from 2008’s level of USD 1.5 billion to USD 2.5 billion in 2014, with the overall market appearing positive for the next twenty years. The aerospace and defense sector represented 23% of total world carbon fiber demand by 2014 in terms of carbon fiber consumption. The aerospace industry is growing at a compound annual growth rate of 19 %, with a paradigm shift toward demand for carbon fiber for manufacturing lighter weight and high resistant aircraft. Besides aerospace and defense, other industrial sectors are also growing though several are, by comparison, still considered niche markets. The industrial sector (excluding aerospace and sports/leisure) grew to 65% by 2014. The other largest growth area for carbon fiber is in filament wound composites for the offshore oil and gas industry. The worldwide actual carbon fiber output reached 76,790 tons by 2014 and it is predicted that the offshore industry alone could require 50,000 tons by 2020. The manufacture of wind turbine blades is the fastest-growing application for carbon fiber usage in the industrial market sector over the next seven years.”
Major Manufacturers of Carbon Fiber:
- Polyacrylonitrile aerospace/high-end carbon fiber:
Toray (largest worldwide manufacturer)
Toho Tenax
Mitsubishi
Hexcel
Cytec
Nippon Graphite Fiber Corporation
- Polyacrylonitrile commercial-grade carbon fiber:
Zoltek
SGL
Challenge:
The major disadvantage is the high production cost, which is limiting the supply, despite growing demand. The major processing steps for the production of carbon fiber usually include spinning, stabilization, carbonization, and sometimes graphitization. Nowadays the polyacrylonitrile precursor represents about half of the production costs, and the equipment cost is about one-third of the production cost. CarbonFiberGeek's ultimate goal is to apply carbon fiber products to all aspects of ordinary consumer life so that carbon fiber products are no longer unattainable, if you have any novel ideas, please let us know, we look forward to hearing from you!
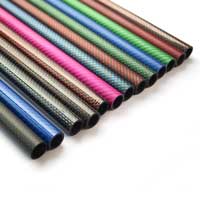
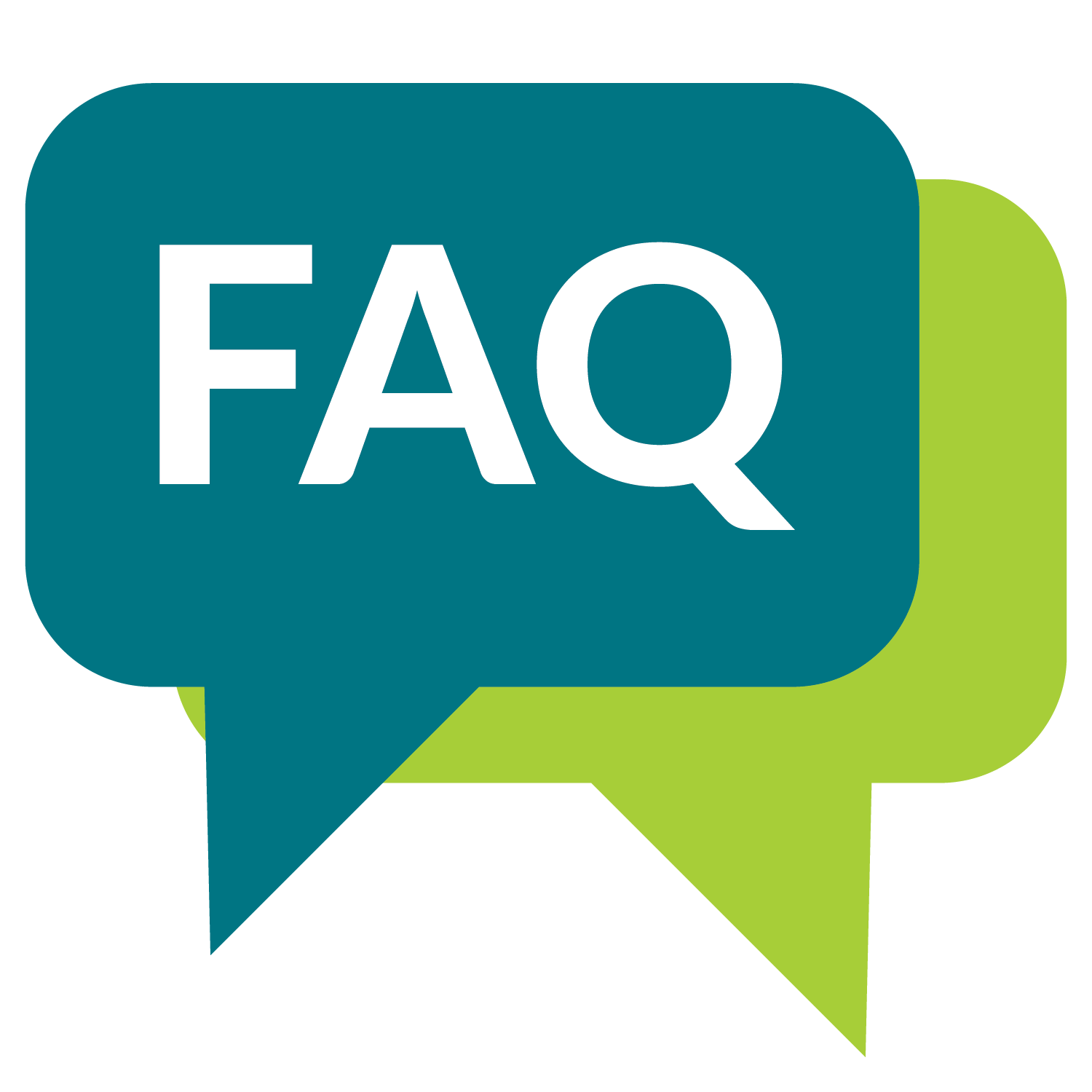